Operational Excellence
Operational excellence itself through superior performance across revenue ( higher output, faster throughput and customer service) and higher productivity (people, material, machines, space). The focus is on what the customer really wants and how to deliver this through continual improvement of value stream processes. Paradigms based on the philosophies of Lean, Total Productive Maintenance and Total Quality Management form the basis for improvement.
KIAP works on a long term basis with clients committed to achieve operational excellence, some of our clients have been on the journey for years, improving performance year after year.
OPEX Journey
This journey is full of continuous improvement & cross-functional teamwork with theme-based working. Themes such as “Strain Free Working” , “Zero Variation” or “MUDA free operations” catch the attention of and create excitement amongst the employees.
The entire movement is built on tangible themes like Position in the Industry, best in class processes and practices, Quality Excellence, Delivery Reliability, Cost reduction, Productivity improvement, Workplace Improvement, etc. To sustain the movement and to ingrain the culture – KIAP also enables the organizations to challenge prestigious awards which will in turn challenge and motivate the teams while giving medium term results to the Business.
The Journey Has Four Main Stages:
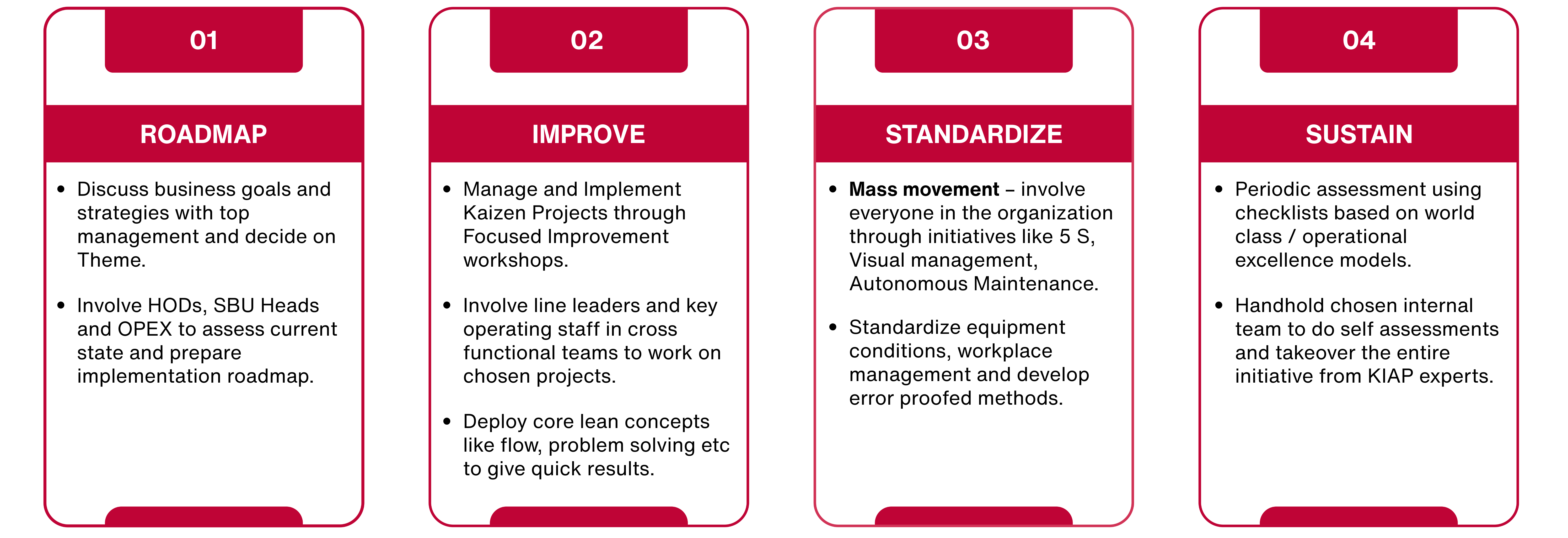
By the end of the program, the organization can expect the following outcomes
- Common goal orientation through all layers of the organization.
- Internal champions capable of managing implementation of improvement projects.
- Continual improvement spirit and concepts inculcated into majority of the employees.
- Significant process improvements completed giving substantial business benefits.
Featured Case Studies