Master Training Program For Career Enhancement with certifications
Lean Champion Certification
Lean is a philosophy, a way of life which espouses “Doing More and More with Less and Less”. The lean paradigm focuses on making the most effective use of available resources (man, machine, material, information) and this is measured through improvement in the parameters of Productivity, Quality, Cost, Delivery, Safety and Morale. The philosophy is industry size and sector neutral and is applicable across manufacturing, service, retail, infra and IT sectors.
About This Program
The founding fathers, Toyota, believe in the kaizen way of implementing Lean and our program follows this same path with emphasis on “Learning by Doing”. The participants are expected to apply their classroom learning of concepts, tools and techniques during the program itself by diagnosing current problem areas in an actual organizational process and focusing on drawing up improvement plan for at least one significant process. The course is therefore split into three spaced out modules with a week’s gap between each of them to facilitate practical application of the learning by doing projects based on actual client situations.
KIAPs vastly experienced lean experts will guide and vet the projects. The participants will be presenting their project work on the final day of the program. There will also be an online test after the three modules are completed to assess the participant’s grasp of Lean concepts.
Lean Champion Certification Program | ||
---|---|---|
Module 1 Lean Foundation, Assessment & Diagnosis
|
Module 2 Lean Tools to Achieve Operational Excellence
|
Module 3 Building Blocks of Sustenance
|
Certification
Those participants who successfully complete the course by scoring atleast 65% in the test and the project assessment will be certified as Lean Managers by KIAP.
Pedagogy
The founding fathers, Toyota, believe in the kaizen way of implementing Lean and our program follows this same path with emphasis on “Learning by Doing”. The participants are expected to apply their classroom learning of concepts, tools and techniques during the program itself by diagnosing current problem areas in an actual organizational process and focusing on drawing up improvement plan for at least one significant process. The course is therefore split into three spaced out modules with a week’s gap between each of them to facilitate practical application of the learning by doing projects based on actual client situations.
KIAPs vastly experienced lean experts will guide and vet the projects. The participants will be presenting their project work on the final day of the program. There will also be an online test after the three modules are completed to assess the participant’s grasp of Lean concepts.
Featured Case Studies
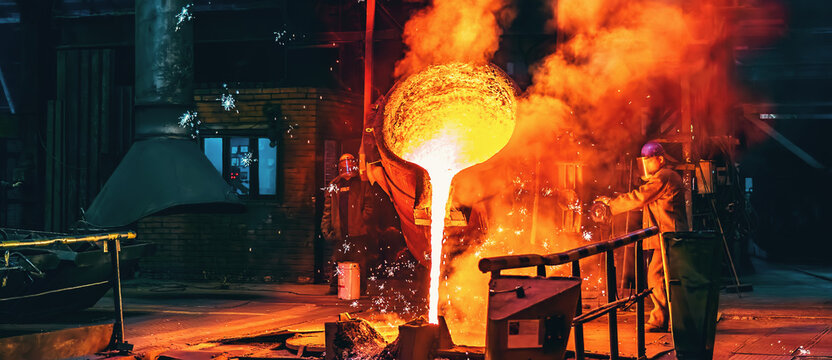
A Leading Foundry reduced 72% of WIP by MUDA Elimination
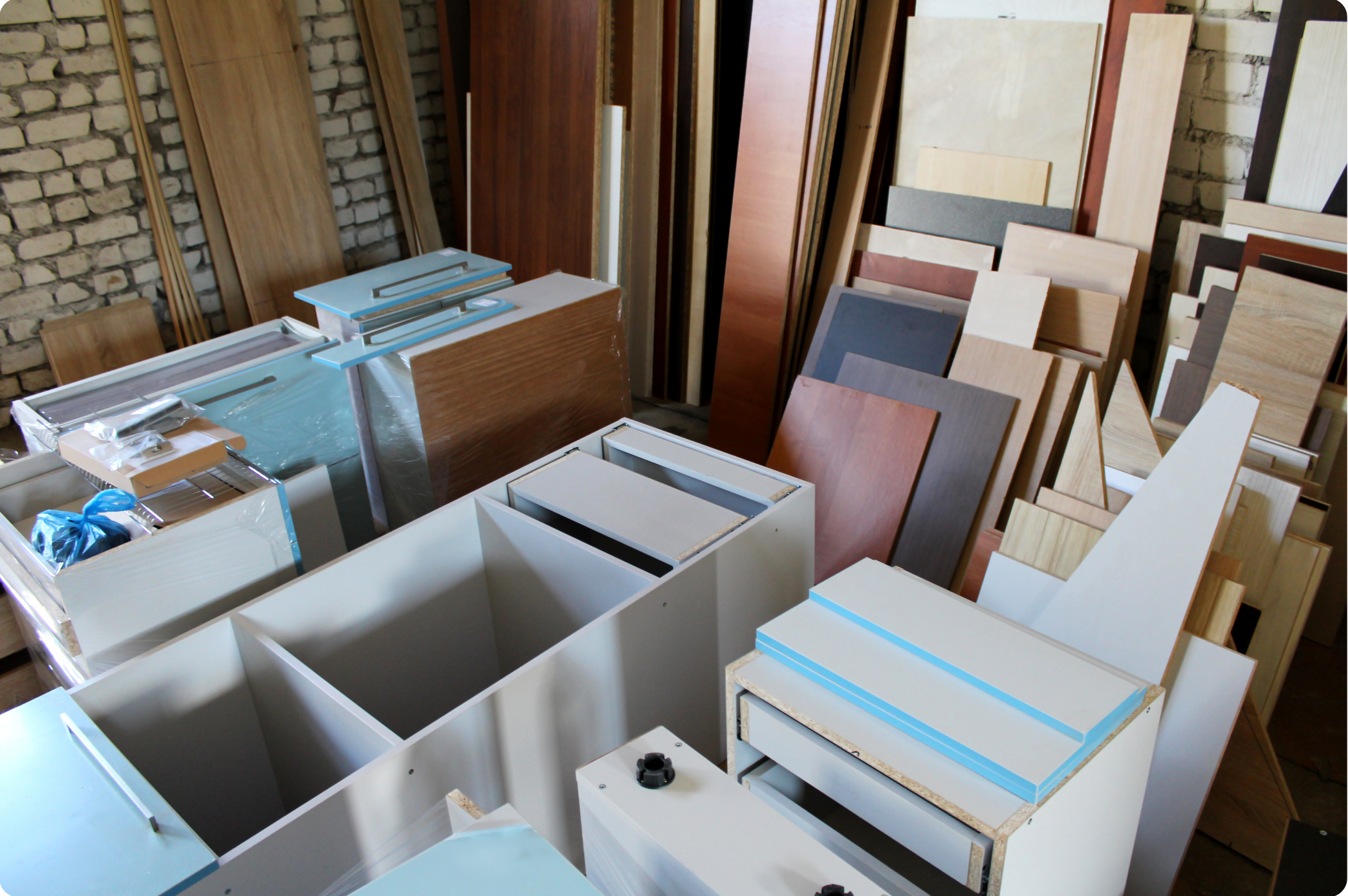
De-bottlenecking in a Furniture Manufacturer to improve output
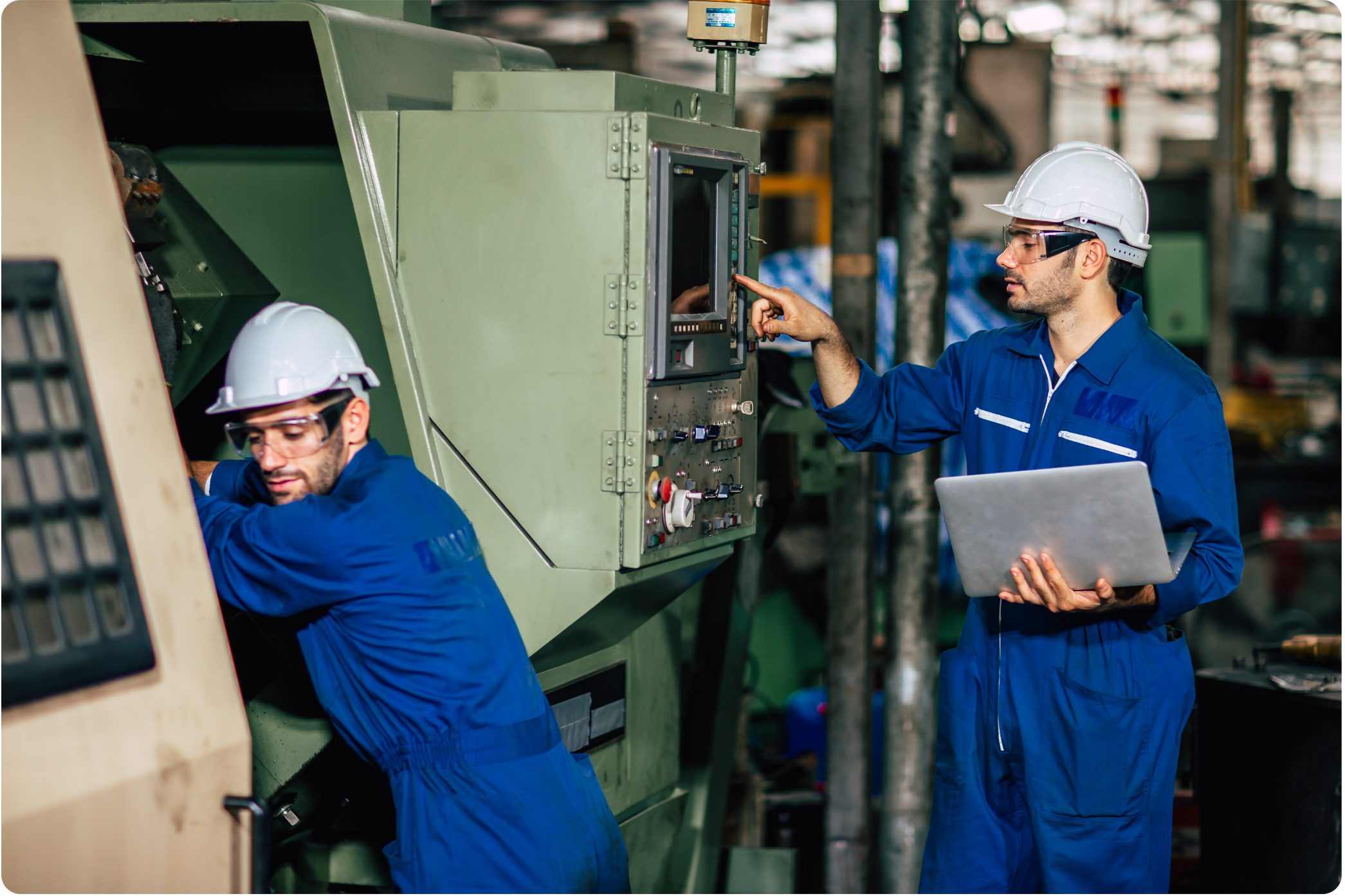
How 90% error reduced by Process Re-design?
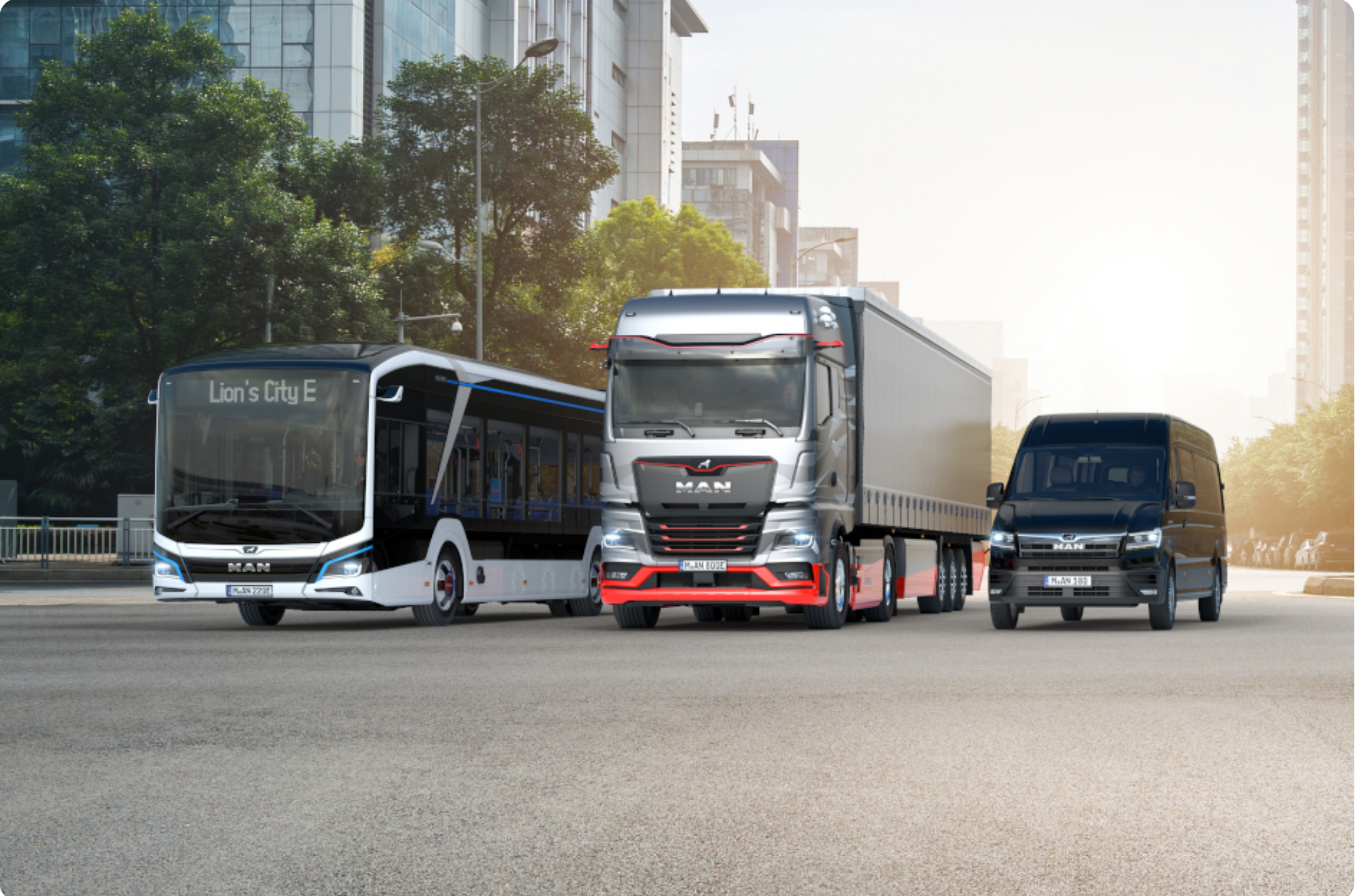
Truck and Bus Body Building – Improve production in short time
Featured Business Novel